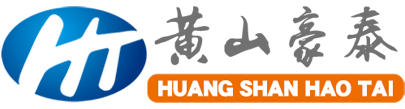
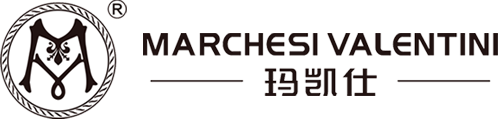
0086 0559-6661188
扫一扫 添加微信
Operating procedures
Requirements for the use of suction plastics
The absorbance is a two-component gel with an activation temperature of approximately 60 degrees. The storage environment temperature should be between 5 ℃ and 30 ℃, and flocculants below 5 ℃ can cause damage. The drum should not be placed directly on the ground, but on wooden supports, especially in winter. The effective period for the absorbability of plastics is not disassembly, but 6 months from the date of delivery.
Main agent: Curing agent=20:1. When the main agent is mixed with the curing agent, it should be kept in a stirring state. Slowly add the curing agent and stir for at least 3 minutes. The amount of glue produced within 4 hours should be used each time. The glue should be glued well.
Spray coating process requirements:
The spraying sequence is end face front line front+line end face, and the flat part can be completed by spraying; The plane of the end face should be sprayed twice.
The activity time between the main agent and the curing agent is 4-6 hours, and the workpiece should be sprayed with adhesive within 4 hours to achieve the best adhesion effect. Otherwise, it is necessary to increase the activation temperature through rubber cross-linking reaction. Although the external aggregation effect is good, the heat resistance performance is significantly reduced. If secondary spraying occurs on the surface of the PVC film, the adhesive marks will appear.
After spraying, the surface is white and dry. The drying time is 30 to 50 minutes (depending on the temperature, humidity, and adhesive quality of the environment).
The ordinary fan is 1.5-2.0 meters away from the workpiece, and humid air is blown away to avoid PVC bubbles caused by high humidity of the workpiece.
In winter, in order to increase the temperature of the workpiece, small insulation can be used to heat the workpiece to 20 to 25 ℃ (temperature exceeding 35 ℃ is prohibited, otherwise deformation will occur). The machine for spraying glue should have an ambient water temperature of no less than 16 ℃.
Operators should wear masks to protect their health.
The use of silicone film in suction molding machine
Select silicone films of different thicknesses based on the characteristics of the workpiece, such as arc value, edge angle, line width, depth, etc.
Due to the continuous heating and stretching of the silicone film, its sagging will increase, and it should be reduced according to the sagging of the silicone film.
In order to extend the lifespan of the silicone film and prevent the quality of the workpiece, the silicone film should be replaced regularly, such as at the front and left ends.
If there are holes or short cracks in the corners of the silicon film, it can be repaired by a silicone and film repair machine. After repair, the compacted weight is flat, and after drying for 24 hours, 240 # sandpaper can be used normally.
Process parameter settings
Distance between membrane pressure workpieces: For narrow and long workpieces with a width less than 10cm, the distance between workpieces should not be less than 8cm, and for workpieces with a width greater than 10cm, it should not be less than 6cm. The distance between the workpiece and the table boundary shall not be less than 8cm. The longitudinal spacing should be in a straight line to reduce airflow resistance.
Workpiece board, the width and length of the board should be 6-10 millimeters less than the width and length of the workpiece, and the edge surface of the board should be rounded with a radius of 3 mm-5 millimeters or a radius of 3 x 45 ° C. To ensure complete injection of PVC film and air between the workpieces, the PVC film should be firmly adhered to the edge of the workpiece. The thickness of the gasket is about 3/4 of the thickness of the workpiece, which is one of the important measures to ensure that PVC is not pulled white.
Set temperature: Based on different PVC films, the set temperature should be between 130 ℃ and 160 ℃. The temperature of ordinary PVC films (compared to smooth PVC films) should be higher, highlighting that PVC films should be lower (to avoid losses, because the temperature is too high).
Assembly time: The preheating time should be from the 1930s to the 1950s (the color of PVC film is different, and the preheating time should also be different. Light color should be appropriately extended, dark color should be appropriately shortened; PVC film thickness should be appropriately extended, and thin PVC film should be appropriately shortened), the vacuum time should be in the 1980s, and the pressure should be preheating time+10-20s. The time to reach the set pressure should not be too long, it should be 5 seconds, to ensure that the end face of the workpiece reaches the activated PVC film and substrate temperature and quickly sticks down, without excessive stretching of the workpiece PVC film (i.e....) instead of running
Set pressure: Set positive pressure to 3.8 bar -4.2 bar, negative pressure to 0.7 bar -0.8 bar, positive pressure+negative pressure=4.5 bar -5.0 bar.
If the workpiece is too thick, it highlights the PVC film. If the thickness of the PVC film is less than 0.3 millimeters, the set temperature should be appropriately lowered, the preheating time should be increased, and the height of the entire floor stool should be raised. The distance between the workpiece and the heating plate should be shortened to reduce or avoid PVC film changes.
Edge trimming requirements
The workpiece processed by the press should be left for 20 minutes (to ensure the initial curing of the adhesive) before edge trimming can be carried out.
After trimming, use special tools to scrape the edges or use 120 # -180 # sandpaper to chamfer, so that the PVC film is lower than the surface of the workpiece. And clean the adhesive marks on the back with alcohol or other diluents. Check the quality when trimming, repair on site if possible, and select and handle separately if not possible.
The workpiece after membrane pressing should be placed face to face and back to back on a flat material rack. 50 pieces per stack, with heavy objects pressed on top to prevent deformation of the workpiece. The storage time should not be less than 24 hours. The time for the membrane pressed workpiece to reach mid-term curing is 24 hours, and complete curing takes 7 days. Therefore, it is necessary to ensure that the workpiece is aged for more than 24 hours before packaging.